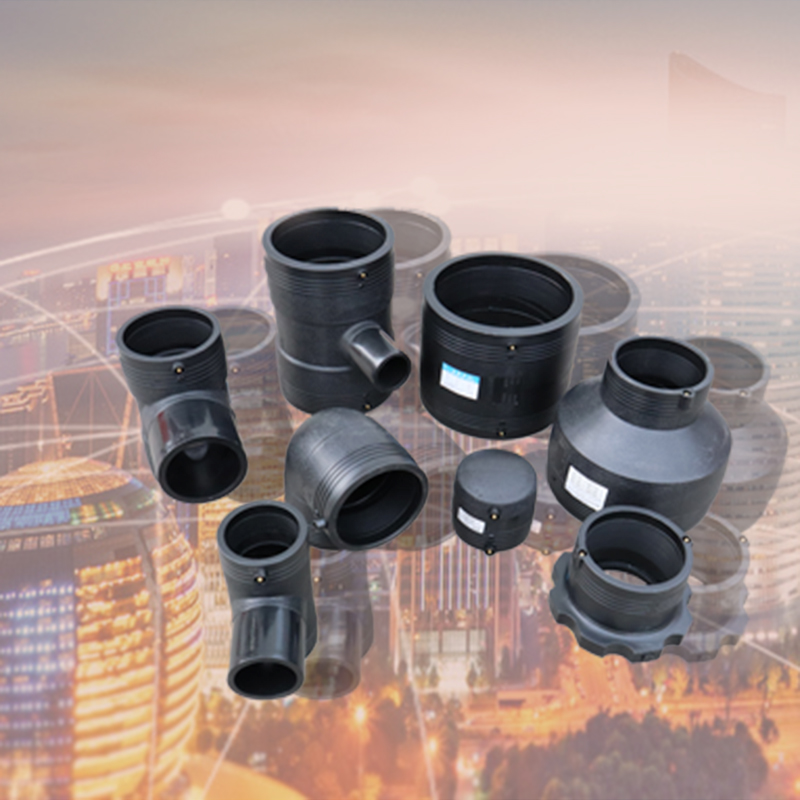
As technology continues to advance, the HDPE (High Density Polyethylene) pipe fittings industry continues to innovate and develop. The latest technological and R&D advances have not only improved the performance and application range of products, but have also advanced the industry as a whole. This article explores the latest technological and R&D advances in the HDPE pipe fittings industry, demonstrating how these innovations are bringing more possibilities and advantages to engineering projects.
I. Advanced material technology
Modified HDPE materials: In recent years, significant progress has been made in the technology of modifying HDPE materials. By adding specific additives and modifiers to HDPE, the abrasion resistance, corrosion resistance and UV resistance of the material are enhanced. These modified HDPE materials perform better in extreme environments and are suitable for more complex engineering scenarios. Case in point: a chemical company used modified HDPE pipes in its wastewater treatment system, which greatly improved the service life and corrosion resistance of the pipes and solved the problem of frequent replacement of traditional pipes.
Nanocomposites: The application of nanotechnology in HDPE pipe fittings has also made breakthrough progress. Through the nanomaterials and HDPE composite, so that the pipe has a higher strength and toughness, and maintain the lightness of the material. Case: In a municipal engineering project, the use of nanocomposite HDPE pipes significantly improved the pressure resistance and durability of the pipes, ensuring the long-term stable operation of the underground pipeline network.
II. Intelligent Manufacturing Technology
3D printing technology: The application of 3D printing technology in the manufacture of HDPE pipe fittings promotes the rapid production of personalised and complex structural fittings. Through 3D printing, complex shapes that are difficult to manufacture by traditional processes can be realised, and production efficiency and product consistency can be improved. Case in point: a research institute used 3D printing technology to successfully manufacture HDPE pipe fittings with complex geometries for specific industrial equipment connections, enabling customised production.
Automated production lines: The application of automated production lines makes the production process of HDPE pipe fittings more efficient and precise. Automated equipment can achieve high-speed, high-precision pipe forming, welding and testing, reducing the impact of human factors on product quality. Case: After the introduction of fully automated production line in a pipe manufacturing enterprise, the production efficiency has been increased by 30%, and the product qualification rate has reached 99.9%, which has greatly improved the market competitiveness.
III. Intelligent monitoring and maintenance technologies
Internet of Things (IoT) technology: The application of IoT technology in HDPE pipeline systems makes real-time monitoring of pipeline operating status possible. Through sensors and data analysis systems, the pressure, temperature, flow rate and other parameters of the pipeline can be monitored in real time, so that potential failures can be detected and warned in advance, and the risk of accidents can be reduced. Case: In a large-scale water supply project, the application of IoT technology has realised real-time monitoring of the HDPE pipeline network, timely detection of water leakage and pipeline breakage, and significant reduction of maintenance costs and water waste.
Pipeline health management system: Combining big data analysis and artificial intelligence technology, the pipeline health management system is able to conduct in-depth analysis of pipeline operation data, assess the health status and remaining service life of pipelines, and provide scientific maintenance recommendations and preventive measures. Case: A petrochemical company has adopted a pipeline health management system to manage the whole life cycle of its HDPE pipeline network, which effectively extends the service life of pipelines and reduces the number of unplanned stoppages and repairs.
IV. Green technology
Renewable raw materials: In response to environmental protection policies, the HDPE pipe fittings industry is actively exploring the use of renewable raw materials to replace traditional petrochemical raw materials. By using renewable raw materials such as bio-based polyethylene, the dependence on petroleum resources is reduced and carbon emissions are lowered. Case in point: an environmental enterprise developed a bio-based polyethylene-based HDPE pipe, which was successfully applied to agricultural irrigation systems, realising the combination of green environmental protection and efficient irrigation.
Recycling of waste pipes: HDPE pipes have good recycling and reuse properties. By recycling, cleaning and reprocessing waste pipes, new pipe products can be made, which promotes the development of circular economy. Case: When a city renews its water supply system, it recycles and processes old HDPE pipes to make new ones, which saves resources and reduces the environmental pressure of waste disposal.
Conclusion
The latest technology and R&D progress in the HDPE pipe fittings industry has not only enhanced the performance and application scope of the products, but also promoted the overall progress of the industry. Advanced material technology, intelligent manufacturing technology, intelligent monitoring and maintenance technology, and the application of green technology have brought more innovation and opportunities to the HDPE pipe fitting industry. In the future, we will continue to focus on technological advances and market demand, and continue to introduce higher performance and more environmentally friendly HDPE pipe fittings products to serve all kinds of projects and help the industry’s sustainable development.